The original hardness of high manganese steel is very low, but the work hardening ability is very strong. The hardness increases during use. The faster the deformation speed, the more significant the hardening effect, and the higher the hardness. Currently, there are the following strengthening mechanisms:
- Dislocation strengthening mechanism: High manganese steel has a large number of mn atoms replacing iron atoms, which significantly reduces the stacking fault energy, making it easy to deform, increasing the dislocation density, forming stacking faults and deformation substructures, and showing work hardening.
- Deformation twin mechanism: After high manganese steel is stretched, lamellar twins appear in the hardened zone, and the hardness reaches hv460. After being hammered with a heavy hammer, layered twins and dislocation tangles appeared up to hv500. During explosion hardening, composite twins appear, the hardness increases, and the hardened layer thickens.
- Deformation martensite mechanism: From a thermodynamic point of view, martensite can be obtained by rapidly cooling the alloy below the ms point, and there is an md point below the ms point, and deformation martensite can be produced due to stress between ms and md. body. Generally the ms point is lower than 200℃. When the mn content is 12%, the ms point is below -230°C, so high manganese steel that is generally deformed at room temperature will not produce deformation-induced martensite. If the carbon content in the steel is reduced to 0.8%, no deformation martensite can be found at room temperature, but δ.θ martensite can appear at a low temperature of -196°C, changing the manganese content in high manganese steel, and the When the manganese content is reduced to 4%, ε.δ martensite is generated after deformation at room temperature. After solid solution of conventional high manganese steel, it is deformed by 50% of the deformation, and the hardness has reached a relatively high value. When the deformation value increases to 35% , it was found that there was a small amount (about 1.4%) of δ martensite, during which the hardness change was inconsistent with the increase rate of δ martensite. Such a large deformation test also indirectly proved that the main reason for hardening was not due to the production of δ martensite. . Previous reports on the discovery of martensite may be due to high-manganese steel being heated at high temperatures in an air furnace, resulting in a decrease in surface carbon and manganese, or insufficient heating and local carbon depletion, which promotes the emergence of deformed martensite. According to this mechanism, there are now reports of controlled surface decarburization of high manganese steel to produce martensite after water toughening treatment, which is used to strengthen the high manganese steel and improve its wear resistance.
- Precipitation phase strengthening mechanism: During the deformation process, as the deformation amount of high manganese steel increases, defects in the austenite increase, and supersaturated carbon aggregates at dislocations, vacancies, stacking faults, twins, etc. to form Coriolis air masses. Impeding slip, deformation heat continues to accumulate, redistributing the segregated carbon and manganese atoms, preferentially nucleating and growing up at defects, forming ε carbides dispersed in the matrix and on the grain boundaries. According to the Olowan mechanism, the interaction between sliding dislocations and dispersed carbide particles increases the critical shearing stress required to force dislocations to pass through the particles, thereby strengthening the austenite.
In high manganese steel with high carbon content (carbon is 1.49%), carbide precipitation was found after 50% compression deformation. Although no carbide precipitation was found in high manganese steel with conventional composition, a reduction in lattice constant was also found, which is equivalent to a 0.1% reduction in the carbon content in austenite. When analyzing high-manganese steel tooth plates with better performance in the national tooth plate evaluation, it was found that a new phase that was not found in the original structure appeared in austenite, which may be deformation-induced ε carbide.
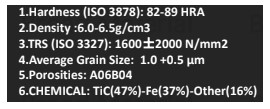
