Hadfield steel invented in 1882 has an enormous capacity for work-hardening upon impact and it is commonly used for railroad components such as frogs and crossings and for rock-handling equipment. It has nominal composition of iron, 1.0 and 1.4 % carbon and 10 to 14 % manganese in a 1 to 10 ratio in accordance with ASTM –A128 specification.
Due to its unique service properties, it has been used widely in a number of applications like rail tracks, dredge buckets, jaw crushers and a number of high impact and wear resistance operations with minor or no modifications in composition and heat treatment.
Many variations of the original austenitic manganese steel (AMS) are available, often in unexploited patents, but only a few have been adopted as significant improvements. These usually involve variations of carbon and manganese, with or without additional alloys such as chromium, nickel, molybdenum, vanadium, titanium, and bismuth.
The mechanical properties of AMS vary with carbon and manganese content. As carbon is increased it becomes increasingly difficult to retain all of the carbon in solid solution, which may account for reduction in tensile strength and ductility. Nevertheless, as the carbon increases above 1.2 %, the abrasion resistance increases, while, the ductility is lowered. The carbon content is usually below 1.4 % and 13 % manganese due to the difficulty of obtaining an austenitic structure sufficiently free of grain boundary carbides, which are detrimental to strength and ductility.
The most popular function of TiC cermet rods is used in manganese wearing part: hammer heads, jaw plates, blow bars,impact plates, liner plates, tooth points, crush rollers, etc.you can add 5% TiC ferro alloys in the casting parts, and the working life is double increased.
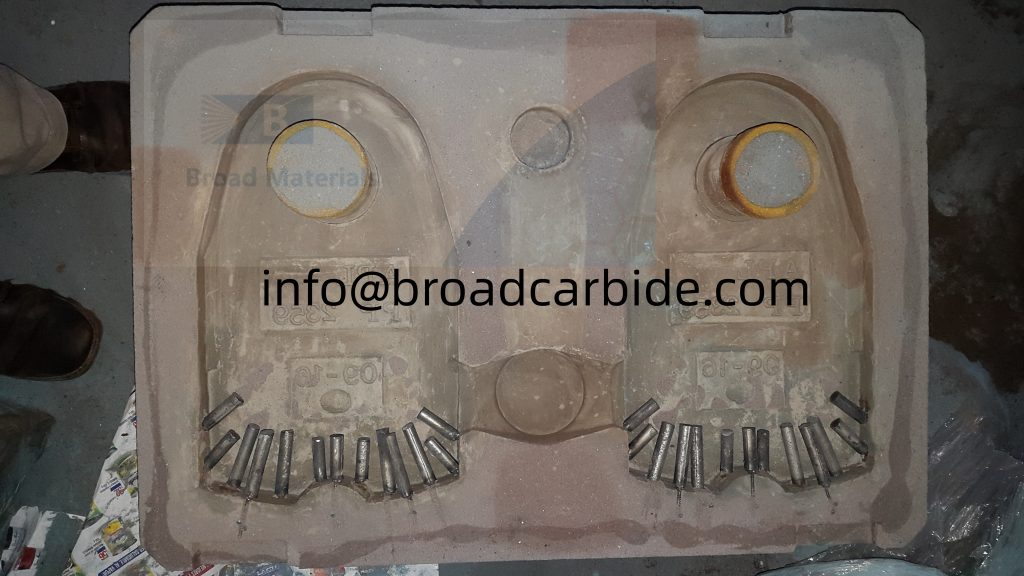