Porosity is one of the common casting defects in casting production. The casting scrap due to porosity accounts for about one-third of the total scrap. Porosity is the gas gathered on the surface of the casting, subcutaneous and internal formation of the hole wall smooth cavity. Generally, porosity is divided into three categories: intrusive porosity, precipitation porosity and reactive porosity.
Cause I. Intrusive porosity. Pouring process of liquid metal casting intense thermal action, so that the sand and core sand in the gas (moisture, adhesive, etc.) gasification, decomposition and combustion, generating a large amount of gas, plus the original gas cavity, these gases partially invade the liquid metal and can not escape the hole produced, known as intrusive porosity. Prevention is as follows:
1, reduce the sand (core) interface gas pressure is the best means. Such as the selection of good permeability, low gas molding materials; control the moisture of the sand and other gas additives, dry mold sand or fast dry sand, do not use wet sand; the application of low gas, slow gas, gas temperature binder; sand (core) to ensure that the drying, drying of the core should not be stored for too long, the use of the sand core every other day should be returned to the oven before use to dry, in order to prevent the core from absorbing moisture, do not use moisture, rusty cold iron and core support; and so on. Do not use damp, rusty cold iron and core support, etc.; exhaust should be smooth, reasonable arrangement of air holes, the use of risers, to improve the exhaust capacity of the casting; pouring in time after the ignition. After ignition, you can hear the burst of gas and the burning flame around the sand box, and after the sand box is removed, you can see the traces of dampness in the lower part of the sand box. It shows that there are a lot of gases produced such as H2, O2, CO, H2S and other gases.
2、After the steel is discharged, let the liquid steel stand for 5-10 minutes, so that the gas in the liquid steel can escape.
3、The pouring temperature should not be too low to ensure that the intruding gases have sufficient time to float up and escape from the liquid metal. Speed up the pouring speed, choose the right type of air tightness, increase the height of the upper sand mold, and improve the static pressure of liquid metal. When setting up the pouring system, attention should be paid to the smooth flow of liquid metal, and the pouring should never be interrupted to prevent the gas from being involved in the liquid metal.
Cause two, precipitation porosity. Dissolved in the liquid metal gas, in the cooling solidification process, due to the solubility of the precipitation of the formation of pores, known as precipitation pores. Precipitation pores are many in number, small in size and round, oval or needle-like in shape. In the casting section is a large area of uniform distribution, mainly hydrogen and nitrogen pores.
Metal, especially in the liquid metal, can adsorb and dissolve a large number of gases. Dissolved in the metal liquid gas, in the low temperature and the external atmosphere when the pressure is lowered, it will be precipitated from the metal, part of the breakaway adsorption to overcome the resistance to escape, part of the metal liquid surface due to the solidification of the resistance is greater than the buoyancy of the formation of air holes. Prevention is as follows:
1, reduce the amount of suction. Clean charge, use clean and dry charge, limit the use of charge with more gas; drying furnace lining and pouring tools, pouring packages to be dried, the best use of liquid iron hot before use, packages with liquid iron, be sure to put the covering agent on the surface of the liquid iron. Ensure that the “three dry”: that is, out of the iron trough, out of the iron mouth, over the bridge to be thoroughly dried; shorten the melting time, to avoid contact with liquid metal and furnace gas, reduce the melting suction and so on.
2, degassing treatment. Available elements to join the degassing method or blowing inert gas, as well as vacuum degassing method.
3, to prevent the precipitation of gas. Improve the cooling rate of castings, improve the pressure of the external atmosphere.
Cause three, reactive porosity. Due to the liquid metal and casting interface between the liquid metal and slag or liquid metal between the internal elements of certain chemical reactions occur between the gas and the formation of holes, known as reactive porosity. Reactive pores are generally uniformly distributed in groups, and often produced in the casting of subcutaneous formation of subcutaneous pores, but also because of its shape is needle-like, also known as pinhole. Such pores appear more in the cast steel parts. After sand cleaning a few pores exposed, heat treatment to remove the oxide skin after more pores exposed.
In production practice found the following image: thin-walled castings of the bottom than the side and above the pinhole (bottom moisture is not easy to evaporate); thick-walled castings are above the pinhole; wet casting than dry type, wet type parting surface, especially more; steel deoxidation of bad pinhole. There are two views on the mechanism of the formation of subcutaneous porosity: one is hydrogen said, the second is carbon monoxide said.
Hydrogen that the liquid steel in the casting of water vapor contact chemical reaction decomposition into hydrogen, part of the escape, part of the dissolved in the liquid steel, so that the hydrogen content in the liquid steel to reach saturation. When the casting solidification, the liquid steel contains hydrogen to be precipitated from the solid phase and was driven to the metal solid – liquid interface, the formation of hydrogen segregation, so that the interface on the hydrogen concentration greatly increased. Especially when the scrap steel contains rust and grease, the hydride content is high. If the liquid steel contains more FeO, then in the casting skin FeO reacts with hydrogen to generate H2O. water becomes non-spontaneous gas nucleus, the liquid steel precipitation of hydrogen to the gas nucleus concentration, the formation of bubbles and growth, and ultimately the formation of pores.
Carbon monoxide theory that when the liquid steel deoxidation bad residual FeO or steel and water vapor reaction to generate FeO, these iron oxides and carbon in the liquid steel reaction to generate CO.
Its prevention methods in addition to gas and deoxidation, minimize hydrogen and iron oxide in steel; strict control of water in the sand; minimize the brush water when modeling; enhance the casting of the exhaust capacity.
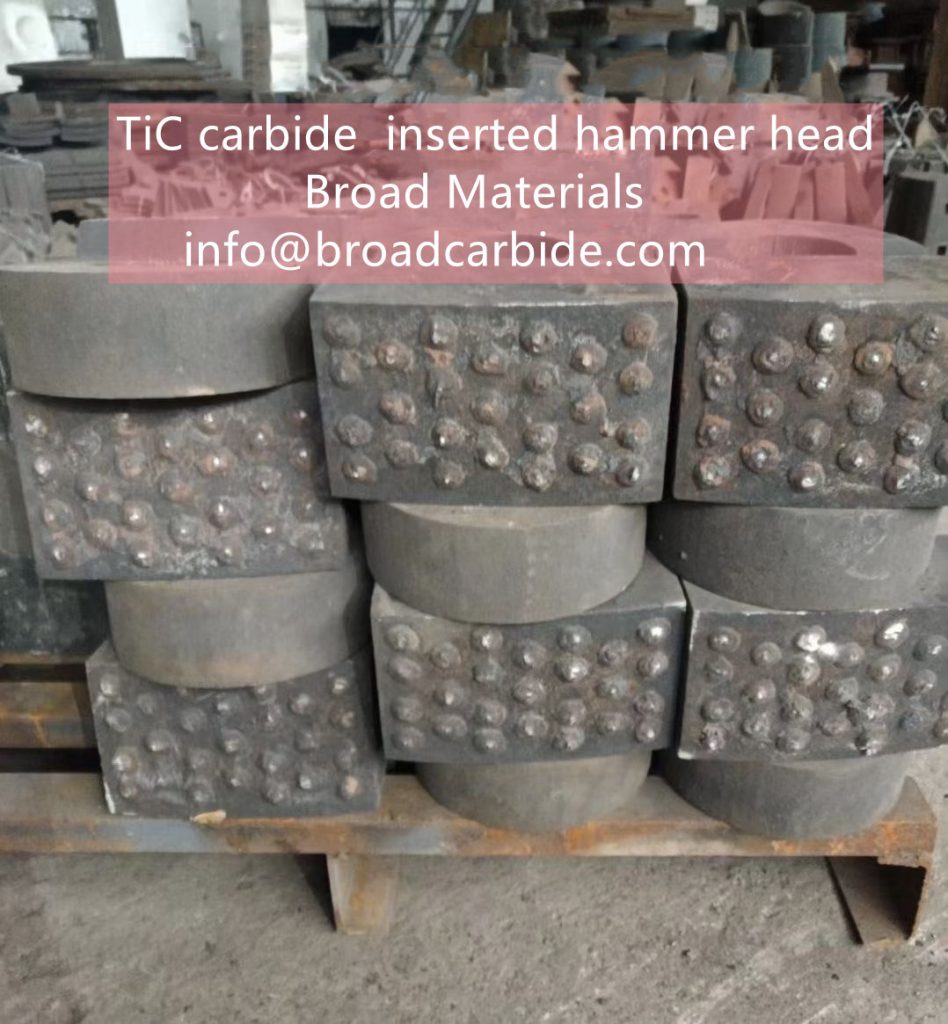